Our Vision
We are the Top-runner of analytical laboratories.
Our certificates are the best choice for practical global use.
Our quality is based on the deep knowledge, diverse experience and good technology.
Our quality consists of consistent quality control system from sample reception to the issue of certificates.
In addition, we practice training programs and PDCA cycle for daily analytical activities.
The head of Quality System Committee
Executive Director Hiroko Suzuki
The High Quality test data
JFRL is an ISO 9001 certified laboratory and have established and is operating a quality management system.
We also obtained ISO/IEC 17025 and JNLA laboratory certifications to part of the test items.
In addition, we have been evaluated for GMP compliance in the pharmaceuticals field and GLP compliance in the medical devices and pesticides field.
Regarding other analytical requests, we have established a system that can provide reliable results by fundamentally satisfying the following requirements for ISO/IEC 17025:
1. Widely accepted and validated test methods
2. Calibrated equipment, and reference materials traceable to national standards
3. Technically competent analyst
4. Ensuring traceability of samples and results
5. Developed testing environment
6. Implementation of Internal Quality Control
7. Active participation of domestic and international proficiency test
cf ・FSSC 22000 guidance on Appendix ⅠA, The following provides additional
information relating to questions arising from the revised requirements
・APLAC Guidelines for Food Testing Laboratories
To provide the reliability data
STEP
01
Client
STEP
02
Reception

Reception
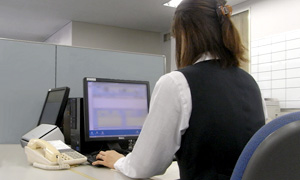
As soon as we receive a sample, we register it in our computer system.Each sample is recognized with eight digit unique number and barcode on the sample label.
Photos of the sample records the current conditions.
The electronic data of the order information is sent to our laboratories.

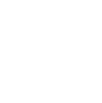
STEP
03
Traceability

Traceability
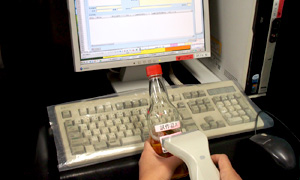
Laboratories section personnel also check the order information and samples.

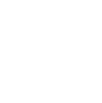
STEP
04
Method Control

Method Control
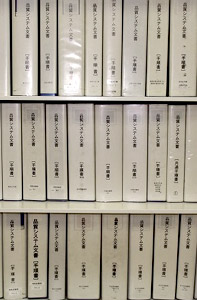
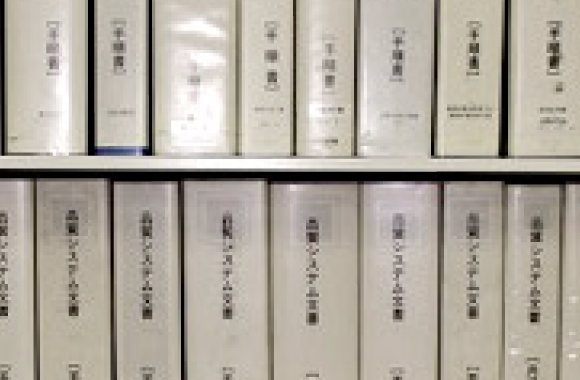
We select the analytical method according to the purpose of clients. Each method is validated and verified by ourselves.

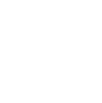
STEP
05
Sample Control

Sample control
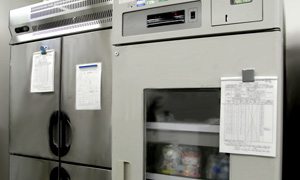
Storage condition is indicated on the sample label.
We keep the sample in a
temperature-controlled refrigerator or freezer to meet requirement of the assays.
Sample preparation for analysisAccording to the matrix, a sample is prepared by the appropriate method.
We develop techniques to prepare various types of samples.


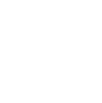
STEP
06
Reference Standard Control

Reference Standard Control
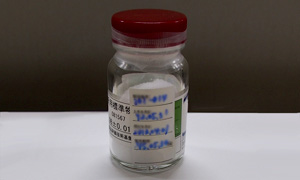
Every reference standard has the management number for traceability.

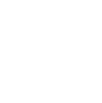
STEP
07
Apparafus Control

Apparatus Control
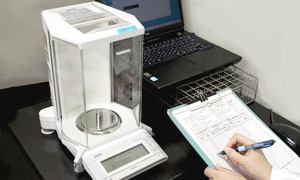
In order to meet requirements of clients, we have a variety of analytical instruments.
Every apparatus has the management number.
We achieved the total equipments control plan (DQ, IQ, OQ, PQ).

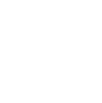
STEP
08
Internal Quality Control

Internal Quality control
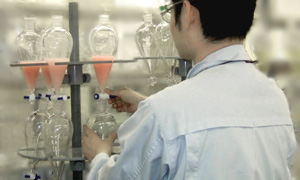
Our personnel are well trained and qualified for all analytical service. To avoid crossing samples, we use the barcode on the sample label. Internal quality control system using reference materials and recovery tests confirms quality of our tests.
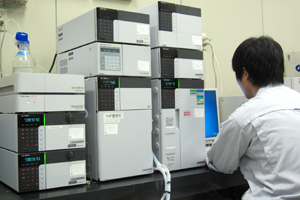
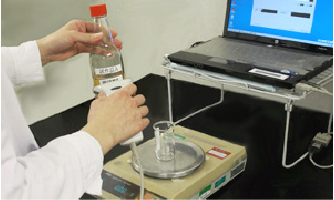

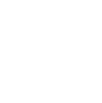
STEP
09
Test Report

Test Report
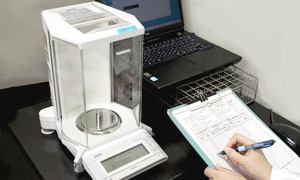
The test data certified by the section head of laboratory are transmitted electronically to the section of analysis documentation. We issue the report and send it to the client.

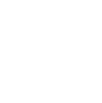
STEP
10
Client
The PDCA cycle of a Quality system
Plan
Quality policy(Our goal)
Training program
Do
Laboratory management
(Sample control / Apparatus
control / Reagent control /
Traceability)
Control of documents
and records
Human resources
Training
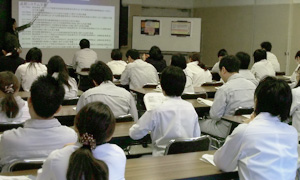
We have the annual training program. The textbook and the trainer is designated by the Training Committee. Also each section has the OJT training program. Our laboratory manager confirms the skills and knowledge of personnel by skill evaluation test.

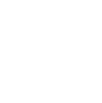
Check
Internal audit
Internal audit
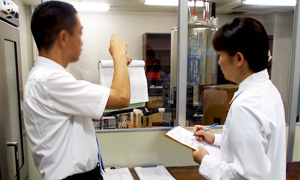
Based on ISO9001 quality management system, the head of Department of Quality Assurance submits an annual audit plan. The trained members audit all sections and confirm the conditions of quality management system.
If nonconformity is found in the audit, a corrective action is done as soon as possible.
PDCA cycle develops our Quality control system.

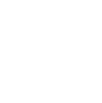
Internal quality control
Proficiency testing Information
From client
From client
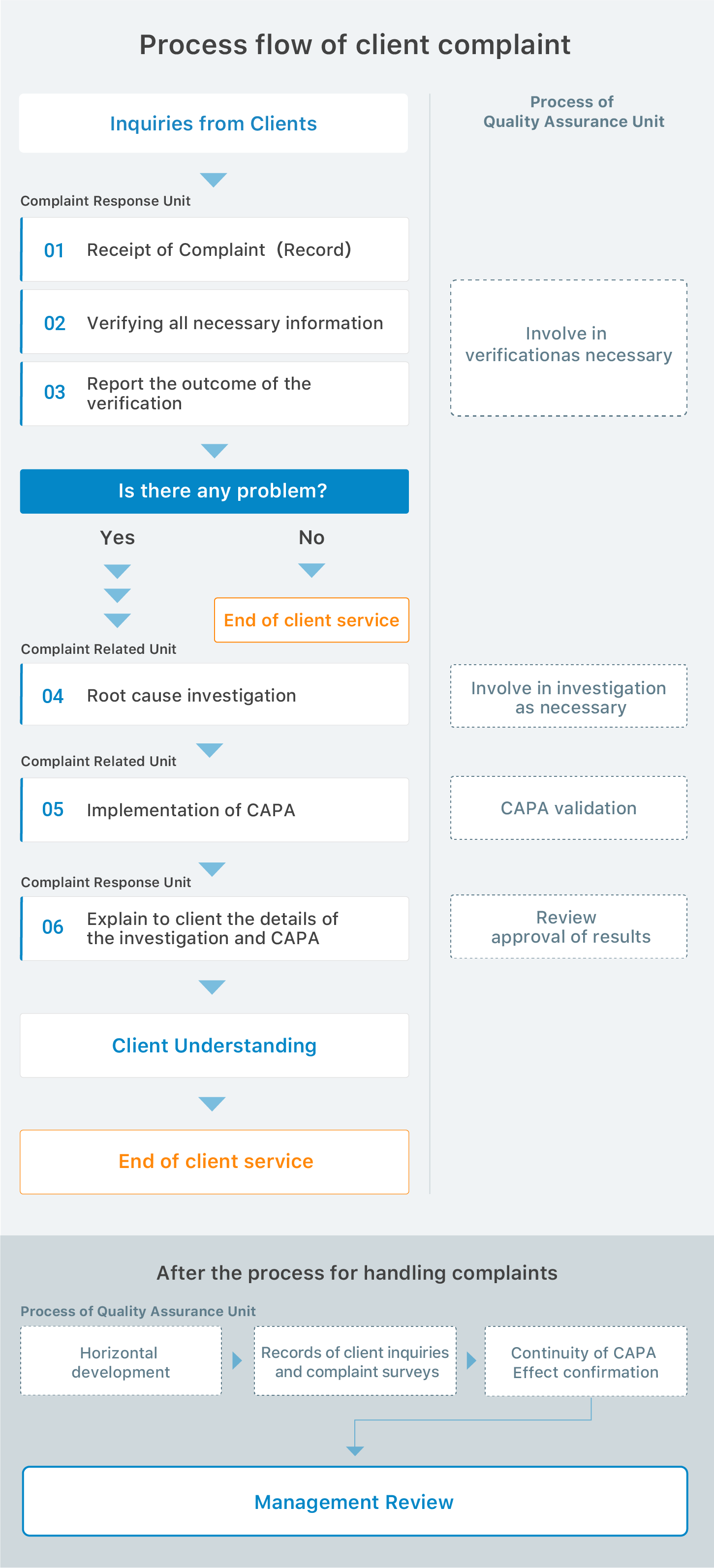

ACT
Corrective and preventive action
Quality System Committee
Management review
- P
-
Plan
Quality policy(Our goal)
Training program
- D
-
Do
Laboratory management(Sample control / Apparatus control /
Reagent control /Traceability)Control of documents and records
Human resources
Training
We have the annual training program. The textbook and the trainer is designated by the Training Committee. Also each section has the OJT training program. Our laboratory manager confirms the skills and knowledge of personnel by skill evaluation test.
- C
-
Check
Internal audit
Internal audit
Based on ISO9001 quality management system, the head of Department of Quality Assurance submits an annual audit plan. The trained members audit all sections and confirm the conditions of quality management system.
If nonconformity is found in the audit, a corrective action is done as soon as possible.
PDCA cycle develops our Quality control system.Internal quality control
Proficiency testing InformationFrom client
From client
- A
-
Act
Corrective and preventive
action Quality System
CommitteeManagement review